Air To Water Heat Exchanger Design Calculations
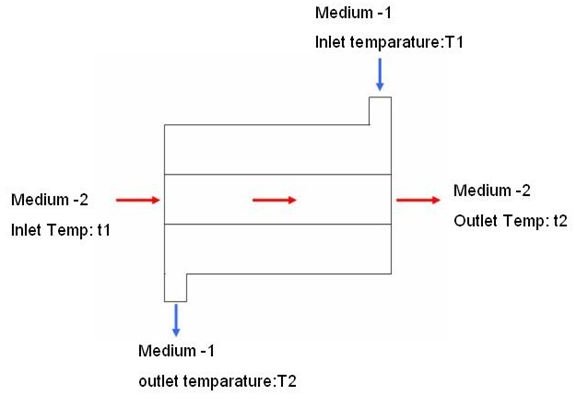
This calculator will help determine which exchanger has enough heat transfer capacity for your system.
Air to water heat exchanger design calculations. Liquids are considered incompressible. The design of a heat exchanger addresses mainly three phases. Calculation assumes true counter flow. Validation of the thermal program once the technological choices made we will proceed to the design of the heat exchanger i e.
Following is the equation to be used. Q m h c ph t hin t hout m c c pc t cout t cin where. L total length of the coil m. Enter the btu requirement temp in temp out and gpm are shaded for hot and cold enter two of the three shaded portions for hot enter two of the three shaded portions for.
Calculation of heat exchanger. The heat transfer area can be calculated after values have been determined or estimated for the required heat transfer rate q. The rate of flow of oil is 1 kg s. Acfm is assumed to be at the average air temperature.
Excel spreadsheet templates for calculating the heat transfer area. The overall heat transfer coefficient. Heat exchanger calculations with the heat exchanger design equation require a value for the heat transfer rate q which can be calculated from the known flow rate of one of the fluids its heat capacity and the required temperature change. During the design calculation of coil heat exchangers the total length of the coil as well as the number of turns and sections are determined.
L f πd р. This allows to have a very high heat exchange coefficient and as a consequence a rather compact heat exchanger compared to other designs which can make them an interesting proposal when space or costs are a constraint. Determining its power size and geometry. It is first necessary to.
D р design diameter of the coil tube m. Fluid properties are used at the average temperatures. When btu requirement is known most applications. Carlson heat exchanger fluid to fluid sizing calculator.
The overall heat transfer coefficient u and the log mean temperature difference for the heat exchanger δtlm based on the values of several input parameters. Air cooled heat exchanger sizing does preliminary estimation of finned area plot size total fan power and air outlet temperature checalc chemical engineering calculations to assist process plant operation and maintenance engineers. Air is assumed to be dry at atmospheric pressure and at zero elevation. N number of turns.
Compulsory titanium on an application with sea water cannot be used on all types of heat exchangers. N l πd р. The outlet temperature of the water is 36 c. The specific heat of the oil is 2 2 kj kg k.
The heat exchanger design equation q u a δtlm can be used to determine the required heat transfer area a for a heat exchanger. The fluid is split into wide but narrow channels in between thin plates. Consider a parallel flow heat exchanger which is used to cool oil from 70 c to 40 c using water available at 30 c.